アディティブ・マニュファクチャリングによる熱交換器設計
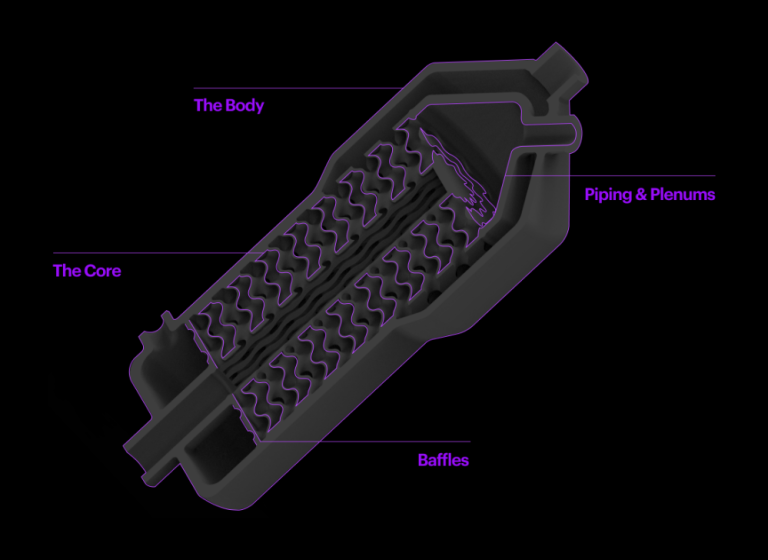
アディティブ・マニュファクチャリングにより、増大している製品要件に対応した次世代熱交換器の設計を行うことができます。この記事では、知っておくべき工学設計の手法とその始め方についてご案内します。
nTopology
August 18, 2022
- 熱伝達用のアディティブ・マニュファクチャリング
- 熱交換器設計の基礎
- 熱交換器設計の目標
- 製造プロセス&材料
- 熱交換器の設計を向上させるアディティブ・マニュファクチャリング
- アディティブ・マニュファクチャリング型熱交換器向けのソフトウェア
熱交換器は、電子機器の冷却や産業施設での熱回収など、様々な熱伝達の用途において重要な役割を担っています。これらのデバイスは、製品・プロセスが期待される寿命の間に意図したとおりに機能することを保証するため、熱管理にとって不可欠です。また、エネルギー生産においても重要な役割を担っています。
しかし、高性能を求められる用途の多くでは、効率やサイズの面で従来の熱交換器の製造方法では技術的な限界に達しています。そこで登場するのがアディティブ・マニュファクチャリング技術です。アディティブ・マニュファクチャリングの設計の自由度は、より革新的な設計を可能にし、熱交換器の性能を最適化する力を与えてくれるのです。
この記事では、より効率的でコンパクトな熱交換器を開発するために、アディティブ・マニュファクチャリングをどのように利用できるかを探ります。
熱伝達用のアディティブ・マニュファクチャリング
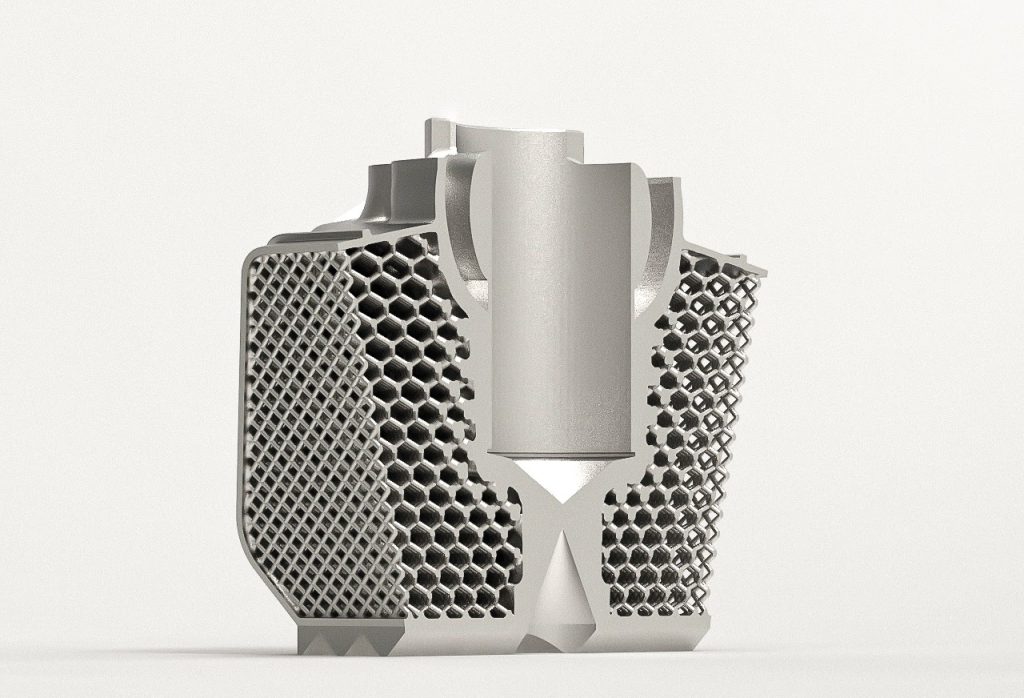
アディティブ・マニュファクチャリング・プロセスにより、エネルギー効率、システム性能、そして熱伝達を向上させるために最適化されたさまざまなジオメトリを作成することができます。新たな技術によって、様々な熱伝達や流動条件に対して最適化された内部形状を持つ、新しいアディティブ・マニュファクチャリング型の熱交換器の設計が可能になるのです。
アディティブ・マニュファクチャリングが熱管理や熱伝達にもたらす主な利点を以下に紹介します。
- 熱交換器を一体化して製造します。アセンブリを1つのコンポーネントに統合することで、故障や漏れの可能性や共通する部位を最小限に抑え、設計の全体的な信頼性を向上させることができます。また、在庫や人件費も削減できます。
- 熱交換器のコアの設計に最適である複雑な三重周期極小面(Triply Periodic Minimal Surface、TPMS)ラティスを構築し、サイズ、重量、性能、製造性の要件を満たしながら、最小の体積に最大の表面積を詰め込むことを可能にします。
- 圧力損失や流量などの特定の性能要件を達成するために新しい形状最適化技術を適用し、従来の手段では製造不可能な、高度に最適化された構造を設計することができます。
熱交換器設計の基礎
3Dプリンターが熱交換器の設計に大きな影響を与えることをより理解するために、熱交換器の主要な構成要素について詳しく見てみましょう。
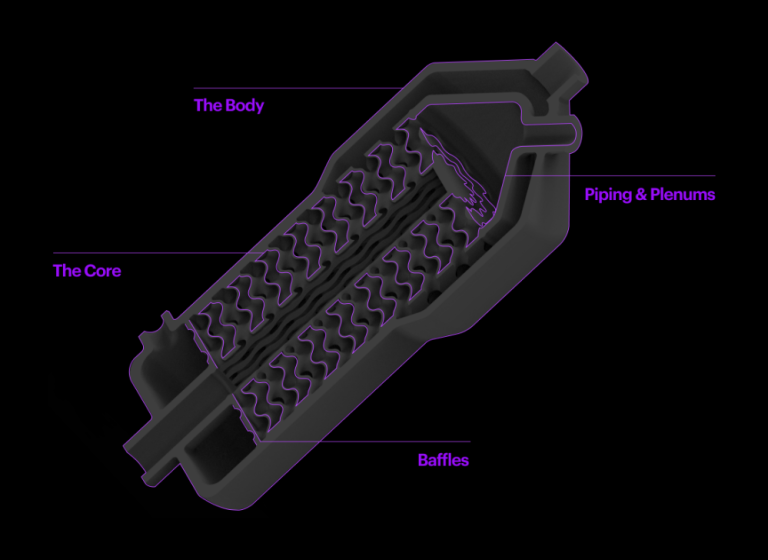
それぞれの熱交換器の構成は異なっていても、基本的な設計のレイアウトは同じです。ここでは、アディティブ・マニュファクチャリング用の熱交換器を設計する際に欠かせない重要な設計上の留意点を紹介します。
ボディ
熱交換器の形状は、用途と利用可能な設計スペースに依存します。従来のピル型、卵型、プレート型でも高い性能を発揮しますが、アディティブ・マニュファクチャリングにより、より幅広い熱交換器本体の形状を自由に検討することができるようになりました。たとえば、イレギュラーな利用可能スペースに適合するように熱交換器の外形寸法を設計したり、熱交換器自体を耐荷重コンポーネントの構造内に埋め込むような設計もできるようになります。
コア
通常、熱交換器のコアはラティス状の構造で満たされています。アディティブ・マニュファクチャリングは、このような複雑な構造を作り出すことができるユニークな技術でもあります。ジャイロイドやダイヤモンド型のようなTPMS構造は、熱伝達のための大きな面積を提供し、流れを自然に分離するため、液体-液体式熱交換器に最高の結果をもたらします。ビーム型のラティスは、単一の領域の固体-液体、または固体-空気式熱交換器にも用途があります。
配管・プレナム
入口と出口の配管とプレナムは、 流れを徐々に熱交換器に導入し、加圧されたバッファゾーンとして機能します。それらの形状は、CFD データ、エンジニアリングの直感、および専門知識を使用して最適化することで、 流れを均等に分配し、圧力損失を減らすことができます。
バッフル
バッフルは冷たい 流れと熱い 流れが混ざらないようにするために必要なもので、一般的にはコアの入口と出口に導入されます。また、ラティスの厚みやセルの大きさを局所的に変えることで、 流れを完全に遮断せずにかき混ぜる「仮想」バッフルを作るという方法もあります。
熱交換器設計の目標
熱交換器の設計を最適化する際に達成しようとする目標は、一般的に3つあります。
熱伝達の最大化
製品の機械・電気化が進み、より大きな放熱が必要になっています。熱交換器の熱伝達率を向上させることは、熱管理の向上につながります。熱伝達率は利用可能な熱伝達面積に比例するため、熱交換器のコアの表面積を増やすと、熱伝達率の上昇につながります。この結果を得るには、熱交換器全体のサイズを大きくするか、コアの形状を調整するか、2つの方法があります。
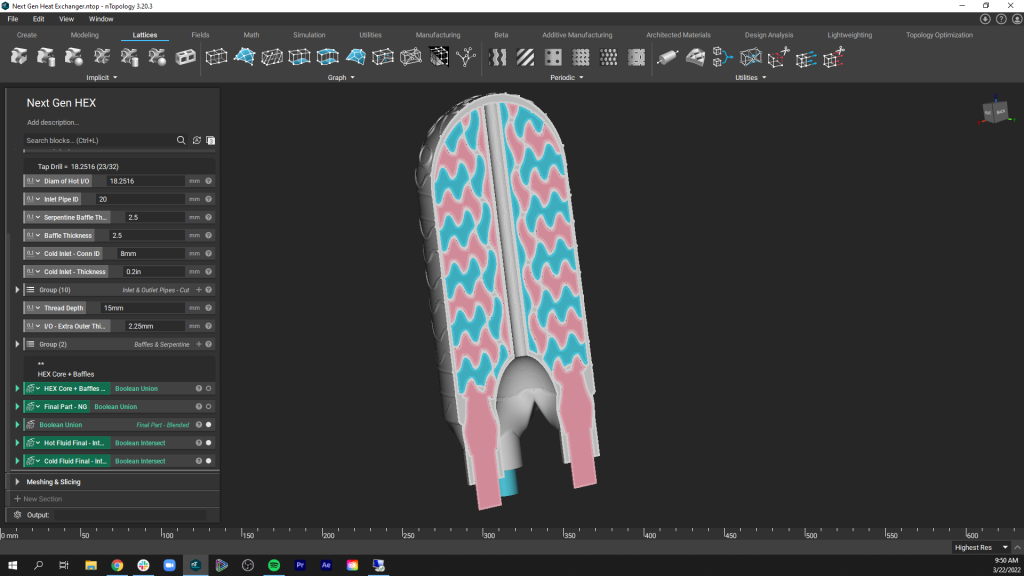
圧力損失の最小化
コアが複雑になると、多くの場合、熱交換器の入口と出口の間の圧力損失が高くなります。それは、システムを駆動するために、より大きなポンプが必要であることを意味します。しかし、スペースやコストの制約、あるいは特定の圧力損失に合わせて設計されたシステムの既存の熱交換器を交換する等、必ずしもこのような選択肢をとれるわけではありません。
熱交換器全体で圧力が一定になるようにするためには、さまざまな技術を用いることができます。均一な流量分布を作る、フローガイドを導入する、ラティス状のコアを操作するなどは、圧力損失を最小にするために有効な方法です。

サイズと重量の最小化
熱交換器を設計する際、サイズ、重量、形状の制約に直面することがあります。例えば、 熱交換器 を搭載するスペースは同じでも、熱伝達率を上げなければならない場合があります。あるいは、冷却チャンネルなどの熱伝達機能を構造コンポーネントに組み込みたい場合もあります。
また、その他の制限に遭遇することもあるでしょう。使用できるスペースがイレギュラーであったり、アディティブ・マニュファクチャリングのコストは使用する材料に比例するため、アディティブ・マニュファクチャリング型熱交換器のコストを予算内に収めるには軽量化が必要であったりします。もし車両に搭載するための熱交換器であれば、可能な限り軽量化する必要があるかもしれません。
このような場合に、軽量化・小型化は必要になることでしょう。
しかしこういった設計目標には、通常では相反してしまうものが多くあります。たとえば、軽量化すると表面積が小さくなり、熱伝達率が低下してしまいます。従来の製造技術では熱伝達、強度、信頼性など、他の要件を満たしながら軽量化設計を開発することは困難でした。ところがアディティブ・マニュファクチャリングの設計の自由性により製品の要件を同時に管理することが可能になり、他の目標を犠牲にすることなく、サイズと重量を最小化することができるのです。
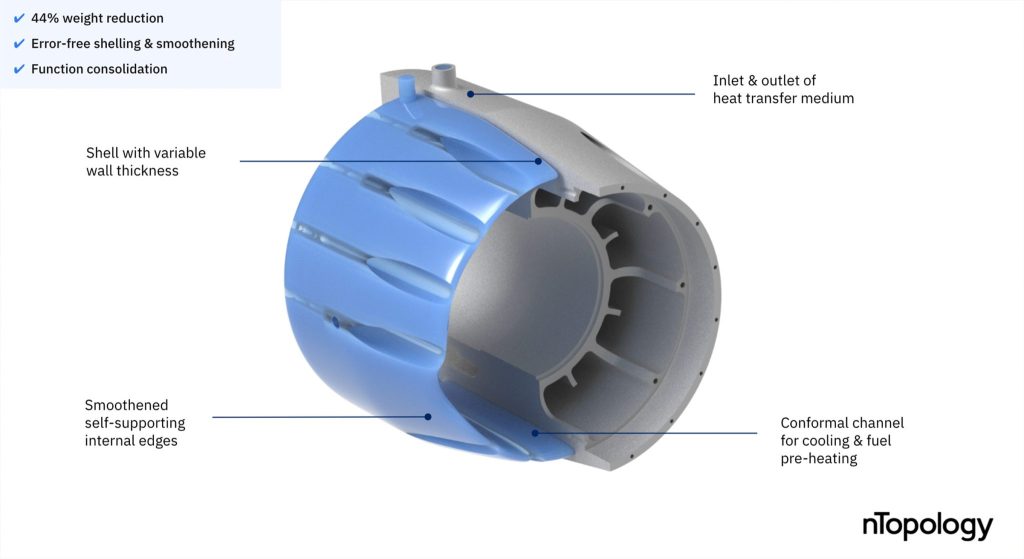
製造プロセス&材料
金属パウダーベッド方式
(Metal Powder Bed Fusion, M-PBF)
金属パウダーベッド方式は、レーザーや電子ビームを使って材料の粉末を溶かして融合させる、一般的な3Dプリンティング技術です。熱交換器の設計では、直接金属レーザー焼結法(Direct Metal Laser Sintering、DMLS)、電子ビーム溶解法(Electron Beam Melting、EBM)、粉末焼結積層造形法(Selective Laser Sintering、SLS)などの方式を使用することができます。
M-PBF方式を用いると、複雑な形状と最大化された表面積を特徴とする、省スペースかつ軽量の熱交換器を製造できます。これは、薄い断面の粉末材料を連続的に積層していくことで、コンピュータのモデルから3D形状を製造する方法です。M-PBF方式は0.1mm以下の極めて薄い壁を作ることができるため、熱交換器の用途に非常に適しています。
銅
銅は、熱交換器設計の材料として可能性があります。純銅は優れた熱伝達性を持っており、マイクロエレクトロニクスから射出成形金型のインサートに至るまで、様々な用途において熱を拡散させるのに理想的な素材です。しかし、この特性によりM-PBFプロセスでは溶融池をきれいに維持することが難しくなります。
さらに、この素材は反射しやすい性質を持っているので、ほとんどの金属AMシステムで使用されている赤色光レーザーでは銅粉のレーザー焼結は困難です。適切な設計エンジニアリングソフトウェアを使用し、アディティブ・マニュファクチャリング方式を慎重に選択することで、これらの課題を克服することができます。
アルミニウム
アルミニウムは熱伝達率が高く、密度が低いため、熱交換器のコンポーネント用として理想的な材料です。これらの特性から、航空機や宇宙船のような重量が重要視される用途に適しています。また、アルミニウムは重量に対する強度が高いため、高温で高い強度を必要とする用途にも適しています。
さらに、アルミニウムは耐腐食性に優れているため、過酷な環境にも適しています。革新的な熱交換器の設計では、より重い金属の代わりにアルミニウムを使用することで、同じ熱伝達をより低い重量とコストで達成できる可能性があります。
熱交換器の設計を向上させるアディティブ・マニュファクチャリング
アディティブ マニュファクチャリングを活用することで、優れた熱交換器の設計を作成できます。
ラティス構造の最適化
ラティス構造は、自然界でもよく見られる構造です。蜂の巣のハニカムパターンや木の幹に見られるような繰り返し模様は、ラティス構造のほんの一例です。これらの構造は、周囲の空間を利用することで、従来の製造方法では作れないような複雑な形状を作り出すことができます。
ラティス構造は、熱交換器のコアの設計に使用されます。アディティブ・マニュファクチャリングのLayer By Layer方式の製造アプローチにより、小さなフィーチャで非常に複雑な設計の中にラティス構造を作成することができます。これらの設計上の特徴は、大きな表面積、高い剛性、エネルギー、吸収性、多孔性を持ち、アディティブ・マニュファクチャリングならばコスト効率よく製造することが可能です。
ラティス構造には複数の種類があります。熱交換器の設計に最も有効なラティス構造は、多くの利点を持つTPMSラティスになります。TPMS構造は、二つの流れを自然に分離し、熱伝達のための大きな表面積を提供し、利用可能な設計空間に適合させることが可能です。さらに、これらの構造は自立していて容易に製造可能であり、流れを2つの領域に自然に分離します。
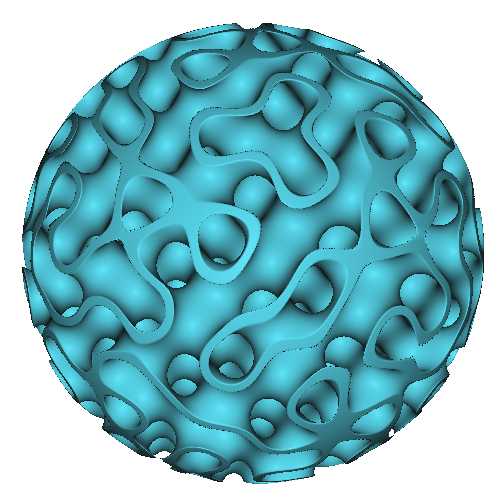
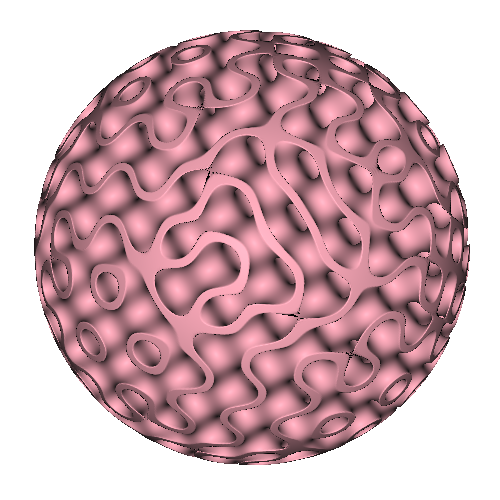
アディティブ・マニュファクチャリング型熱交換器のコアを埋める構造として最も一般的なジャイロイドTPMS(左)とダイヤモンドTPMS(右)。
標準的なTPMSのコアには、ジャイロイド型とダイヤモンド型の2種類があります。これらの熱交換器用ラティス状コア構造は、さまざまな用途で効果を発揮します。構造を選択する前に、動作温度、重量要件、利用可能な設計スペース、製造コストなど、さまざまな要因を考慮する必要があります。
ビーム型ラティスは、固体から液体や空気に熱を伝える際に有効です。
フィールド・ドリブン・デザイン
シミュレーションの「古典的」なアプローチは、デザインを作成し、それを解析するためにシミュレーションを実行するというものです。このプロセスは受動的なもので、このシミュレーションから直接ジオメトリを生成することはできませんでした。
先進のエンジニアリング設計ソフトウェアでは、シミュレーション結果を、設計を生成するための重要な変数として使用できるようになりました。これは、従来のシミュレーションのアプローチを逆転させ、まずシミュレーションを実行して熱交換器内部の流れの向きを明らかにし、その周囲にジオメトリを作成するものです。フィールド・ドリブン・デザインの手法を活用することで、これを実現することができます。
このフィールド・ドリブン・デザインのアプローチは、複雑な部品ジオメトリを生成・制御する優れた方法であり、シミュレーションからあらゆるポイントで設計パラメータを制御することを可能にします。
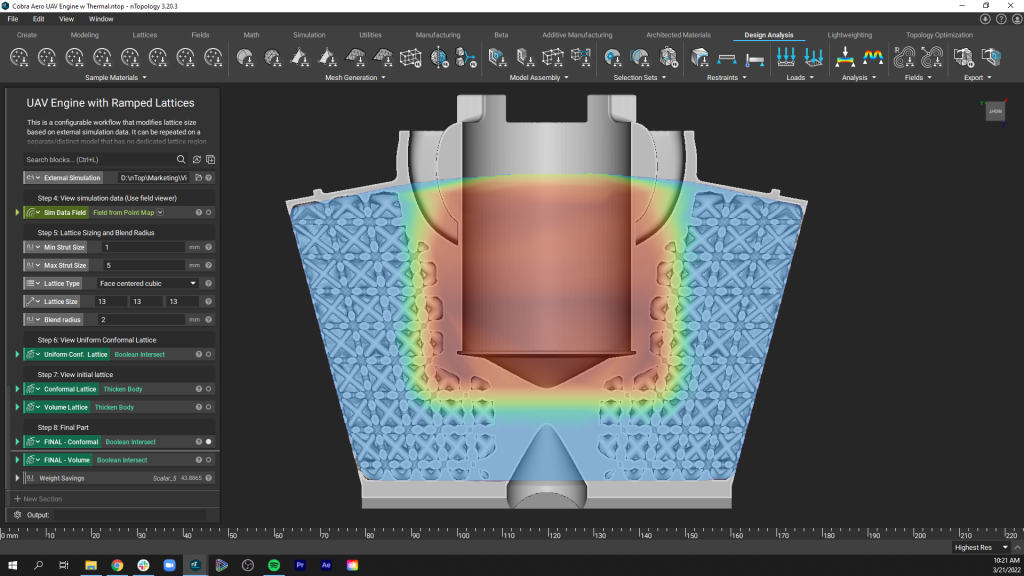
軽量化
軽量化は、多くの熱交換器設計のもう一つの目標で、航空宇宙などの産業においては特に重要となります。そしてその場合、その熱交換器はどのような用途でも最後まで性能を発揮する必要があるため、慎重に設計されなければなりません。アディティブ・マニュファクチャリングであれば全体の強度と構造的完全性を維持したまま、重量を減らすことができます。これは、熱交換器の設計が厳しい環境下で性能を発揮できることを意味します。
設計時間
あなたのチームは、より良い性能の製品をより短時間で開発するというプレッシャーに、これまで以上にさらされていることでしょう。しかし旧式のソフトウェアを使用している場合、適切なアディティブ・マニュファクチャリング設計を合理的な時間で開発することに苦労しているかもしれません。手動プロセスが設計プロセスそのものを遅らせてしまい、そしてその間、他のチームは熱交換器設計の完了をただ待っているだけということになってしまっている可能性もあります。
アディティブ・マニュファクチャリング型熱交換器向けの設計ソフトウェア
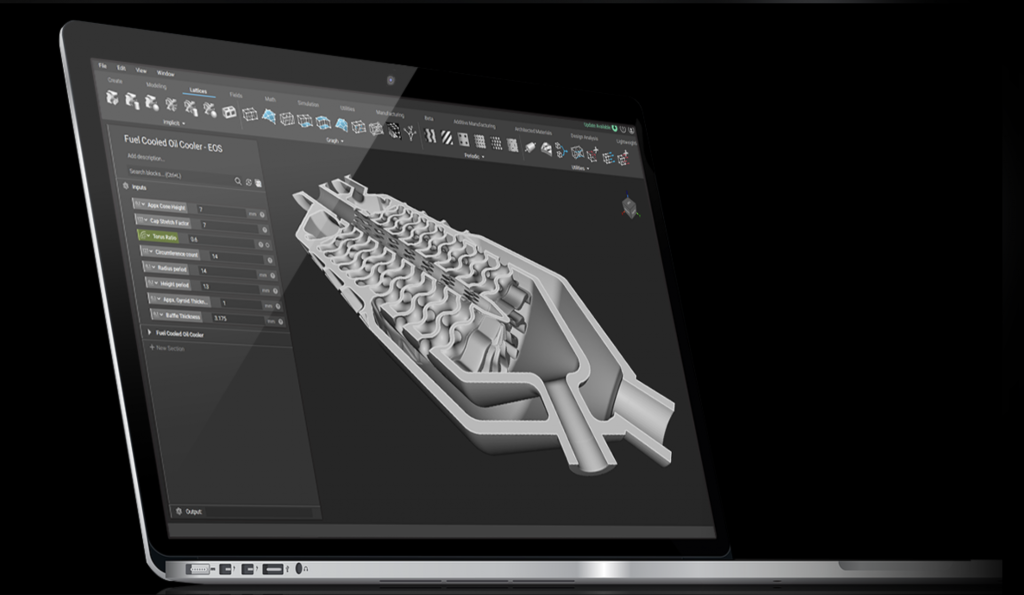
従来のCADソリューションで複雑な熱交換器のコアを開発しようとした場合、いくつかの問題にぶつかったことがあると思います。革新的で複雑な熱交換器の開発を可能にするためには、以下のような機能を持つソフトウェアが必要です。
- ・TPMSやラティス構造の制御を可能にするツールを搭載
- ・CFDシミュレーションツールに接続して検証可能、またはシミュレーションツールを内蔵
- ・CFDおよび熱FEシミュレーションを使用して設計を推進。
- ・堅牢で信頼性が高く、再利用可能な方法で設計変更を行うことが可能。反復設計プロセスをスピードアップし、アディティブ・マニュファクチャリング型の熱交換器の開発をコスト効率の高いものにする。
3Dプリントによる熱交換器の製造は、過去にない最先端の技術です。nTopologyのエンジニアリングソフトウェアは、アディティブ・マニュファクチャリングの利点を最大限に生かしながら、コンパクトで高性能な熱交換器を製造することを可能にします。
重要なポイント
- 熱伝達の最大化、圧力損失の最小化、軽量化により、熱交換器の設計を改善することができます。
- 熱交換器の設計は、軽量化、ラティス状コアの採用、テストシミュレーション結果の活用などを利用することで改善することが可能です。
- 適切な設計ソフトウェアはアディティブ・マニュファクチャリングの利点をもたらし、熱交換器の性能を最適化することが可能となります。